Delta Controls Orcaview Download Youtube
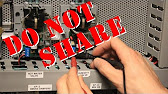
We have several methods to communicate our PC with the Delta PLC’s, and many users don’t know some of them.On the other side, every time is more difficult to found RS232 serial ports in the computers, and the USB to RS232 converters are not as much trustable as they must, because of that I would like to list our alternatives to that problem:Direct communication PC to PLC:1. PC RS232 port to PLC RS232 port using the wiring DVPACAB2A302. PC USB port to PLC RS485 port using the device (Delta USB-RS485 converter).3. PC Ethernet port to PLC (need compatibility with high speed bus)Communication PC to PLC trough Delta HMI (Direct Link):The direct link capability in Delta HMI is used to communicate with the PLC and HMI with one only wire.
Furthermore this capability have been improved lately and now is possible monitor both of them at the same time using only one wire. Direct Link function trough Standard USB wire (WPLSoft and ISPSoft)2. Direct Link function trough Ethernet (WPLSoft and ISPSoft)Exactly the same feature is available with the new DOP-B HMI’s with Ethernet embedded, really helpful for remote support.3. Direct Link function trough USB host (WPLSoft only).All systems are Win XP / Win 7 compatibles, so now there’s no reason to do not communicate with Delta PLC. I am needing make upload program from the PLC but i not established communication bteween plc and pc, I am using WPL-Soft version 2.45 and windows 10, but when i am make connection with the plc, show up for me erro time out. Because i don’t sucessful with the conection.I am select the “Port COM” correct, and i am using the cable serial RS 232 x USB ( the cable i am using normally in other PLCs of the others brands).I need more other software or other driver for connection with the PLC DVP14SS2 between PC?Automation Technician.
DELTA PRODUCT CATALOG 2017 2 CONTENTS Delta Controls Delta Controls is one of the largest manufacturers of building automation controllers, with more than 300 service providers in over 80 countries. For more than three decades, Delta Controls has offered dependable and user-friendly building control solutions for commercial. Flight status description. Skip to main content.
New DOP-B series HMI was integrated into a machine with DVP-SS PLC and VFD-M. New logic is developed for some I/O’s and parameters are passed through HMI.HMI is set to communicate with Delta-RTU. Data is transferred to PLC D registers.Problem- Data transfer is sluggish(slow). And HMI has error-3 and error-5 repeatedly.Please help in communicating PLC and HMI on Modbus RTU protocol. As I feel some instructions of Modbus are needed in my programming.Awaiting your valuable response.Regards,Fareed. Greetings of the day!Thank you so much for your valuable reply. I have already contacted the distributor and I have myself tried to minimize this delay and I have got a very positive result.i.e., No printing delay after receiving the printing command but in this case I have to make printing size setting very small around which prints only 1/6th of my print screen and also do not contains any graphical representation but only some text and a few boxes.
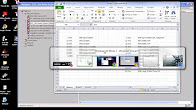
But for page size around half of the A4 size delay is still happening. The Distributor customer support engineer said that this much delay will be there it can be minimized.So, I think there is no programming leak of any kind in LD and HMI because it works if I only change the printing size of the printing screen.But I hope that you people know some effective way to minimize it may be by using some other printer Inkjet or Laser type.ORIs there any other way through which I can connect any printer as per your suggestion directly or indirectly (via PC) to HMI?ORIs no. Of HMI screens have anything to do with this delay?I have made total 8 Printing screens out of which four are for monitoring purpose only for four types of jobs with different performance ratings and other four screens are for printing purpose which gets printed for selected job type.Please provide me with your opinion and advice for the same.I am waiting for your valuable advice.Thanks and RegardsM.M.Saifi. I do not find any detailed expanation on how to set PC, HMI and PLC to make them communicate by “DirectLink”. I can not force them to do that. I connected PC USB to DOP-B 101S USB and they communicate normally.
I connected DOP-B 101S COM1 RS232 to PLC DVP12SC COM1 RS232 38400bps 7N1 and they communicate normally too. But then I try to get PLC online monitoring through HMI USB in WPLSoft after couple of seconds it shows error message “Timeout”. I selected DirectLink (USB) in WPLSoft Options/Communication settings/Communication Type. Is there any other setting what I could miss?
Is DirectLink working on bouth HMI COM1(RS232) and COM2(RS232/RS485)? What could be wrong?Plese help me to solve the mistery:). Hello,In a RS-485 connection between a PC and a DVP-14SS2 wiht expansion module DVP-16SP, I have a problem reading the memory address from DVP-16SP inputs. Programming with WPLSoftware we use X20 and X21 from DVP-16SP but when we want to read them from the PC we can not find them. With a C# program, we read X0-X7 inputs without problem reading 8 points starting at address 400. So we program to read 8 points starting at address 420 to read X20-X27 but it doesn’t work. Can you help us with that?Also, we have problems with LRC calculation we are doing as it is said in the program manual but it doesn’t work, any suggestion?Thanks in advande for your help.
We are using DVP14SS PLC with 2 add on A to D modules. The PLC communicates with HMIs using RS-485 and with “Elipse” Scada using RS-232 Port. We have noticed that Scada’s communication with PLC frequently times out. The timeout period in Scada is 700 msec.
Delta Controls Orcaview 3.4 Download
We have seen this problem in 2 applications. For one application we are using “BAFO USB to RS232 adapter” for PC - PLC communication and in another case PC’s RS-232 port is directly communicating with PLC’s RS-232 port, using special cable provided by Delta dealer(Cable length 7′ Max). We are using Modbus Protocol for communication and the settings are ASCII, Even Parity, Data 7 bit and 1 stop bit, baud rate 9600.Because of communication failure the Scada application is running erratically. Hi Delta,Currently, there is no problem when using the direct link ethernet to modify the ladder diagram in ISPsoft 1.0.3.But there is a list index out of bounds (0) while using the WPLsoft 2.20.11 on direct link ethernet.I confuse what number should I put at the port number on WPL while ISP does not need any port number to be set.Secondly,When the HMI port is set to 12346, ISPsoft could detect the plc properly, but when I change this number, it is a mess. Any suggestion?
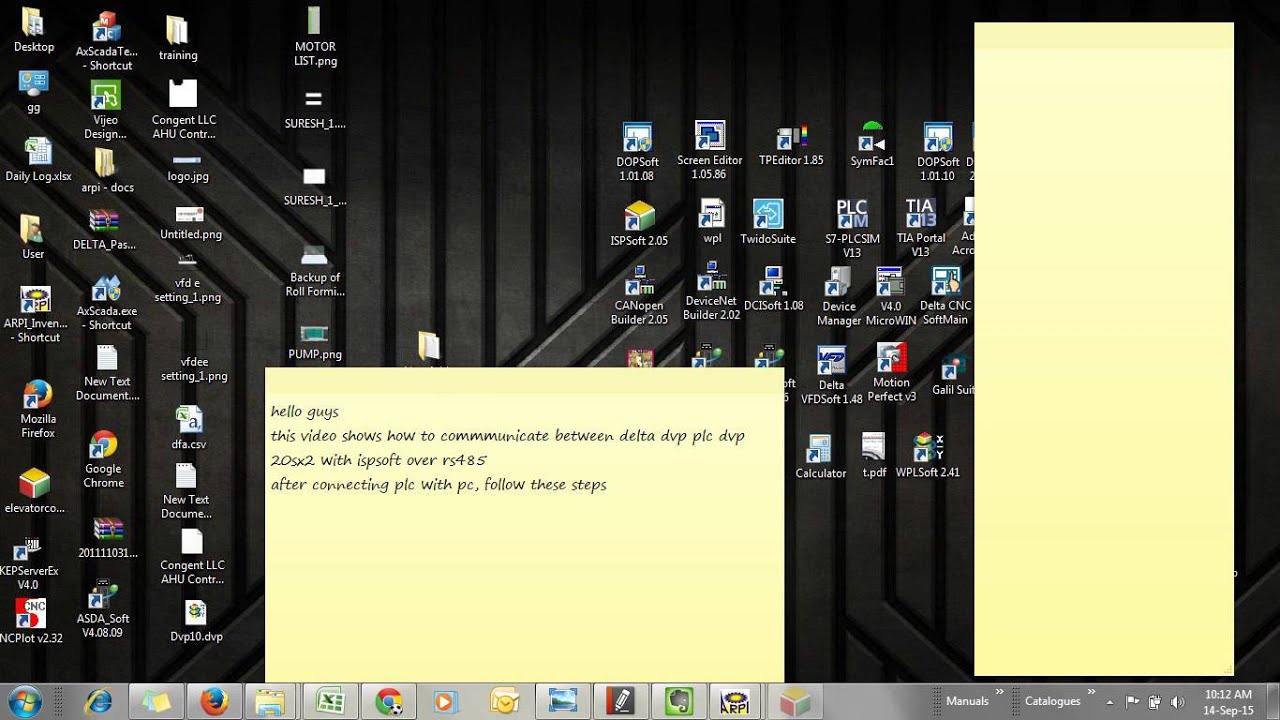
Since there might be a case of multiple HMIs with multiple PLCs so I need to set different HMI port.Third,The Delta DOP support of ModbusTCP, Could I view this as a replacement for IFD9506 which I might be able to communicate with DVP?Lastly,I now confused why the HMI have a port number differ from the standard modbusTCP which is 502.Thank you for your assistance. Hi HeryantoThe only port able to communicate trough direct Ethernet link today is 12346.We know about that limitation, but we´re still working to solve it.Why is this one, and not 502?? Frankly speaking, I don´t knowRegarding If DOP can be a replacement for IFD, I don´t think soThey are completely different products, but yes, both are able to communicate with DVP PLC.I recommend HMI in machines that needs an interface, and IFD, If you already have the interface, but you want to add yor machine to the net. Hi,I have one DOPB10E, connected to ES2 at com2 and another ES2 at com3.What I would like to do is to view and edit the two (com2 and com3) PLC’s Registers and HMI register’s via DOP’s ethernet.I will writing a windows program to interface with the user.1. Running WPLsoft connected to DOP’s ethernet to program one PLC via DOP’s com is not a problem.But having two DOP’s coms connected to PLCs, it is a problem.2.
For short term goal, How to alter the DOP’s register via it’s ethernet?Thats for now.Thank you for your guidance.